The last 2 years have undoubtedly been highly pressured times for UK retail, bringing challenges of a scale that businesses in this ever-competitive sector could have scarcely imagined as pre-pandemic.
The COVID-19 accelerated processes of modernisation for the last mile home delivery sector that were already long in motion. While, for instance, a significant uptick has been seen since 2020 in the percentage of UK retail sales that take place online, this is a trend that has been gradually building since 2006.
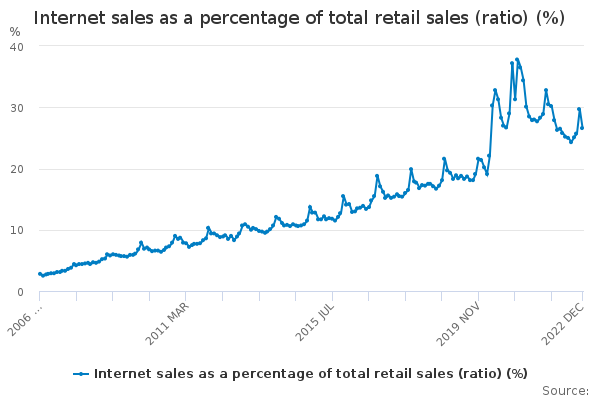
Your retail business may have been gearing up for heightened online sales a while before the pandemic, or you might be only just significantly modifying your strategy and making major investment in your infrastructure for home delivery.
Either way, your firm is likely to be highly appreciative of the most relevant loading bay equipment for making such services easier to provide.
What relevant solutions can we bring you right now?
Among the loading bay equipment that we are proud to supply and install for our retail customers re-jigging their processes for the new logistics era, are the dock levellers that remain an imperative part of many premises for levelling the difference in height and distance between a warehouse floor and a docked vehicle.
To this end, we are pleased to continue to offer industry-leading swing lip, telescopic lip and manual solutions. Of particular relevance, however, for the trucks and vans customarily involved in the provision of home delivery services, might be our combi-dock levellers.
Our user-friendly, safe and energy-efficient combi-dock levellers can be used with articulated vehicles as “standard” dock levellers incorporating a telescopic lip. When, however, there is a need to load and unload vans, these dock levellers can be used with only the centre section of the lip or board sliding out.
Furthermore, our combi-dock levellers’ built-in load capacity sensors help to prevent delivery vans from becoming overloaded, so could otherwise so easily occur at this time of notably increased demand for home delivery.
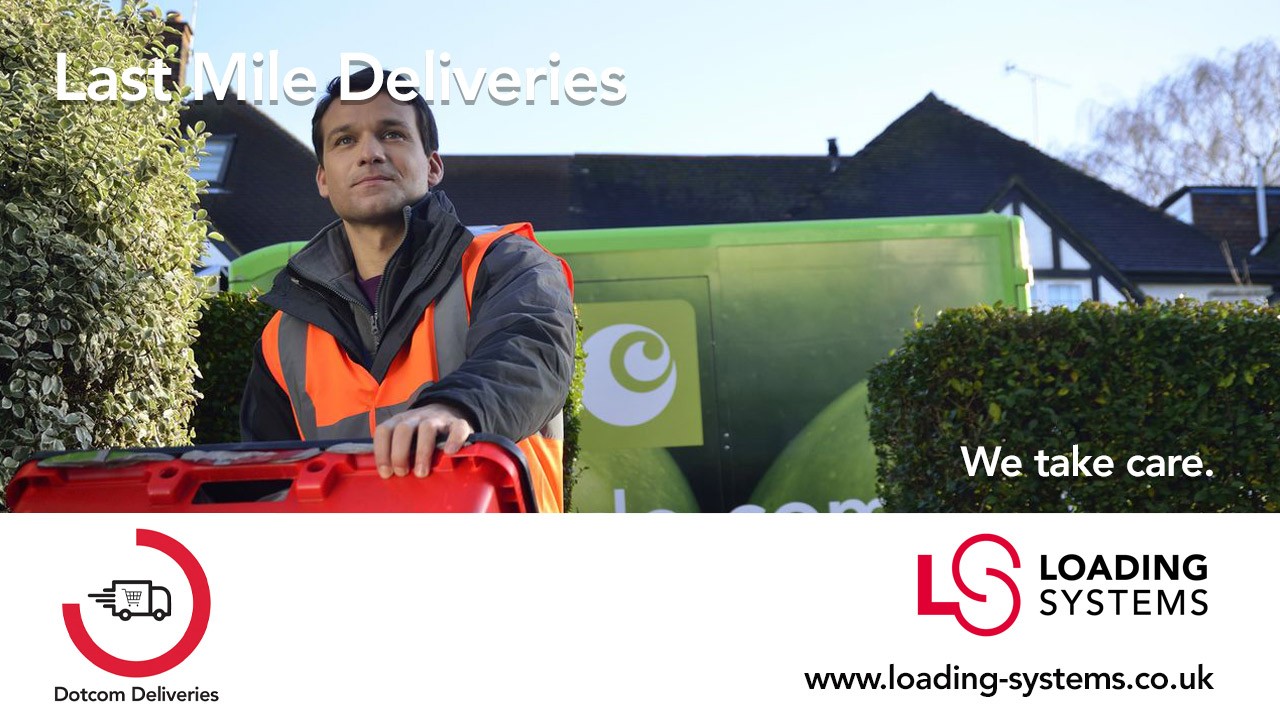
Introducing ‘the Fandango’
As well as new van dock levellers and combi-dock levellers, however, we are delighted to be able to present ‘the Fandango’, otherwise known as the Universal Bridge Plate Lifting Table.
In the complicated world of 2020s logistics, it is typical for various different vehicle types to be used for delivery and distribution. This brings the risk of loading bays being unable to interface with all of the vehicles that may conceivably encounter them.
The innovative Fandango changes this, allowing for the loading and unloading of vehicles of any type from a single loading bay – thereby minimising the number of loading bays required in a warehouse.
The Universal Bridge Plate Lifting Table works on the principle of allowing businesses in the supply chain to unload goods from a standard or double-deck trailer loading bay, followed by quickly switching the dock’s configuration for the loading of a home delivery van.
The result can be much-improved operational efficiency, lower costs and significantly reduced risk to the health and safety of warehouse operatives. Then, there’s the other likely outcome, of infinitely greater satisfaction for the end recipients of your firm’s home delivery services.
5 ways we genuinely ‘take care’ of your loading bay equipment
But our reputation as a manufacturer, supplier and installer of solutions for loading bays like those at your own premises is not founded on our equipment alone.
That’s because we are also renowned for our highly proactive approach to maintenance, which has never been of more pressing importance than it is amid the stresses and strains posed to many firms’ operations by the COVID-19 era.
Keeping your firm’s supply chain operating smoothly is naturally crucial in any conditions, given the considerable potential cost to your business of almost any period of downtime.
This is why we take such an all-encompassing approach to loading bay maintenance here at Loading Systems, including both preventative and reactive elements.
But what are just five specific aspects of our maintenance approach that you will be thankful for when your company teams up with Loading Systems?
1. Through our complete Service Agreement
Take out a Service Agreement with us, and you will be able to greatly minimise the chances of damaging disruption to your business’s operations resulting from failed loading bay equipment, whether that equipment in question is a dock leveller, the ‘Fandango’ or something else entirely.
Our Planned Preventative Maintenance programme incorporates the regular servicing that will reduce the overall ownership cost of your loading bay equipment and give you vital day-to-day peace of mind.
2. By complying with all relevant legal and safety requirements
Everything that we do here at Loading Systems is in accordance with the relevant EN standards and Machinery Directive Guidelines, including – where applicable – CE marking.
The law states that loading bay equipment should only be inspected, serviced and maintained by specialised and competent persons, which is something you can certainly be assured of with us.
3.By providing an Extended Warranty
Such is our absolute confidence in the quality of the parts and services we provide, that a five-year no-quibble extended warranty is provided with all of our new equipment.
This means that even if any components covered by the warranty do fail or malfunction, you won’t be charged for either parts or labour when our engineers arrive to replace the problem item.
4.Our commitment to changing parts prior to failure
One of the key aspects of our Planned Preventative Maintenance approach is our use of a process known as Change Parts In Time (CPIT).
This philosophy is very much what it sounds like, with components that are known to have certain life expectancies – such as wearing parts and hydraulic hoses – being replaced during service before they have the chance to fail. This naturally lessens the likelihood of downtime for your company.
5. By being better prepared than any other maintenance provider
The very nature of unpredicted events is that they are unforeseen, and your firm may not be as prepared as it perhaps should be to quickly resolve the problem on its own.
That won’t be the case when you team up with Loading Systems for loading bay maintenance. Our engineers’ services can be sought on a 24/7 basis, and when the service van arrives, you can be assured that it will be fully stocked with the spare parts and equipment required to fix most problems that could conceivably arise with your loading bay equipment.
Life’s easier, less stressful and more productive for organisations that place their trust in Loading Systems’ know-how in not only loading bay equipment, but also the relevant accompanying maintenance services.